Mastering the Balance Between Supply and Demand
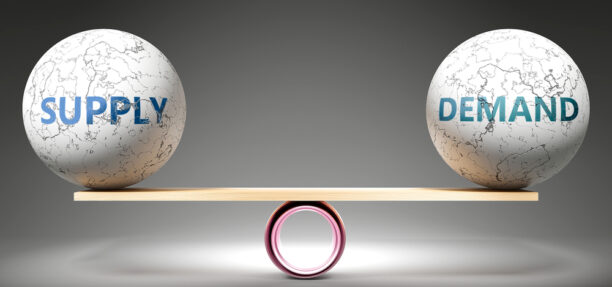
Balancing customer demand with supply chain efficiency is a key challenge for propane retailers. With the right strategies, you can ensure a smooth operation that meets customer needs while also keeping costs low. Here are some key factors and strategies to consider when managing propane supply and demand.
Understanding Customer Demand
To balance demand and supply effectively, it’s important to understand customer demand. Propane demand can vary based on several factors, including season, weather conditions, and customer usage patterns. For example, demand often peaks during the winter months when people heavily rely on propane for their heating needs.
One way to understand demand is to analyze past data. Look at historical trends in customer orders and usage to predict future demand. This can help you plan for peak periods and ensure that you have enough supply to meet customer needs.
Optimizing Inventory Management
Efficient inventory management is key to balancing demand and supply. You need to ensure that you have enough propane on hand to meet customer orders without overstocking. Overstocking can lead to increased storage costs and the risk of unsold inventory.
To optimize inventory management, consider implementing a just-in-time (JIT) system. JIT inventory management involves receiving and storing inventory as needed, thereby reducing excess stock and associated costs. This approach requires close coordination with suppliers to ensure timely deliveries.
You can also use technology to track inventory levels in real-time. Smart meters and sensors can monitor propane levels and provide accurate data on current inventory. This allows you to make informed decisions about ordering and restocking.
Streamlining the Supply Chain
A streamlined supply chain is essential for efficiently meeting customer demand. Review your supply chain processes to identify areas for improvement. Look for bottlenecks or delays that could impact your ability to meet customer orders.
One way to streamline the supply chain is by working closely with suppliers. Establish strong relationships with reliable suppliers to ensure timely deliveries and reduce the risk of disruptions. Consider diversifying your supplier base to mitigate the impact of any single supplier issue.
Additionally, optimize transportation and logistics to improve supply chain efficiency. Ensure that delivery routes are planned to minimize fuel costs and delivery times. This can help you fulfill customer orders more quickly and reduce operational expenses.
Enhancing Customer Communication
Effective communication with customers is essential for balancing supply and demand. Keep customers informed about their propane levels and delivery schedules to properly manage expectations and avoid disruptions. Provide timely updates on any potential delays or changes in supply.
Consider using digital tools to enhance customer communication. Email and SMS alerts can notify customers when their propane levels are low and remind them to schedule a refill. Customer portals or apps can also provide real-time information on delivery status and account details.
Adapting to Market Changes
The propane market can be influenced by various external factors, including economic conditions, regulatory changes, and shifts in energy preferences. Stay informed about market trends and be prepared to adapt your strategies as needed.
For example, if there is a growing demand for renewable energy sources, consider exploring propane alternatives that align with customer preferences. Being proactive and responsive to market changes can help you maintain a competitive edge.
A Strategic Approach
Balancing supply chain efficiency with customer demand in the propane industry requires a strategic approach. By optimizing inventory management, streamlining your supply chain, enhancing customer communication, and adapting to market changes, you can achieve a balance that successfully meets customer needs while still maintaining solid operational efficiency.