A Comprehensive Guide to Organizing and Documenting Monthly Safety Meetings
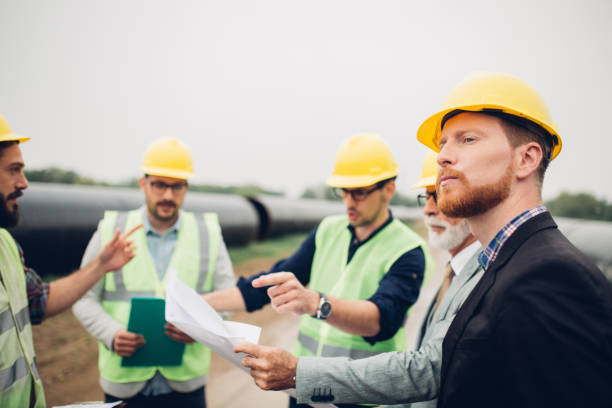
Propane marketers have many responsibilities, including meeting regulatory compliance requirements and ensuring the safety of their team members. Regular safety meetings are essential to fulfill these obligations and document compliance.
Recommended Frequency for Propane Safety Meetings
To maintain safety standards, propane safety experts recommend conducting safety meetings on a monthly basis. However, the frequency may vary depending on individual company policies and procedures.
It is also advisable to hold safety meetings whenever internal safety manuals are updated or modified. The more frequently these meetings are conducted, the better ingrained the safety processes become in the mindset and routines of team members. Depending on the company’s specific needs, meeting more than once a month might be more suitable.
Planning Out Safety Meeting Topics
The key to successful safety meetings lies in proactive planning. Creating a calendar and outlining topics in advance can minimize potential barriers to hosting safety meetings.
Consider seasonal relevance when determining meeting topics, focus on refresher training when necessary, review initial training topics during employee onboarding, and utilize safety incidents as teaching opportunities. A well-organized schedule of topics ensures that each meeting is productive and informative.
Choosing the Optimal Time for Safety Meetings
When scheduling safety meetings, it is important to consider the availability and convenience of safety leadership staff and employees. A morning meeting before drivers embark on their delivery routes may be the most efficient option.
Flexibility is crucial, whether conducting meetings in person, remotely, or utilizing a hybrid approach. Hybrid meetings offer the opportunity for greater attendance, as well as the ability to record and distribute the meetings for team members who are unable to attend. Alternatively, hosting monthly lunchtime meetings can foster team rapport, enhance employee retention, and allow for the dissemination of vital safety information.
Initiating the Planning Process
To start implementing safety meeting plans:
1. Consider creating a calendar for the next six to twelve months. This baseline will facilitate future planning, making it easier in subsequent years.
2. Gather and evaluate relevant training materials, ensuring alignment with the company’s policies and procedures manual.
3. Incorporate materials from Certified Employee Training Programs (CETP) and regulations such as NFPA 54 and NFPA 58.
By documenting safety meeting plans and follow-ups, comprehensive records can be maintained for future reference.
Documenting Safety Meetings
The old adage, “If it isn’t documented, it didn’t happen” rings true when it comes to safety meetings. Diligent documentation is essential, including recording the date, topics covered, safety materials discussed, and attendees.
Organize and store these documents systematically to ensure accessibility when needed. Proper documentation is critical for liability protection and risk management.
Importance of Metrics and Follow-Ups
Tracking safety meeting attendance and conducting follow-ups are vital to mitigating risks and ensuring employee safety. Imagine a scenario where an employee, absent during a critical safety meeting, makes a serious error due to a lack of information.
Companies expose themselves to significant liability and potential legal ramifications without proper tracking and follow-up procedures. By keeping tabs on attendees and following up with absentees, all employees can receive the necessary safety information, regardless of availability during a specific meeting.
Simplifying Safety Meetings for Increased Efficiency
Convenience plays a significant role in the successful implementation of safety meetings. To streamline the process, consider partnering with an external safety provider who can supply monthly topics and materials, thereby saving both time and effort.
Third-party providers offer an invaluable resource, allowing companies to focus on other critical tasks while ensuring comprehensive safety coverage. These materials can be utilized for team quizzes, providing insights into additional training needs and identifying areas of excellence. Future safety meeting calendars can be planned in collaboration with the provider, incorporating previously missed topics and areas requiring improvement.
Promoting Safety as a Habit
Safety training should extend beyond initial onboarding and certifications. Regular safety training and meetings are essential to comply with regulatory requirements. By following the steps outlined in this guide, propane companies can establish a culture of safety, prioritizing the well-being of their customers, employees, and the overall industry.
TankSpotter.com and PropaneSafetyPro.com: Enhancing Safety and Compliance
Two valuable resources, TankSpotter.com and PropaneSafetyPro.com, offer propane businesses comprehensive solutions to improve safety and compliance. Tank Spotter provides a complete risk management solution, helping to lower risks, increase compliance and safety, and improve service and sales management. PropaneSafetyPro offers safety training and consulting services to ensure that propane firms possess the necessary expertise and knowledge to uphold the highest safety standards. Propane businesses can leverage these resources to overcome industry challenges, embrace technology, adopt visual documentation, and prioritize safety and efficiency.