When and How to Invest in Equipment Upgrades
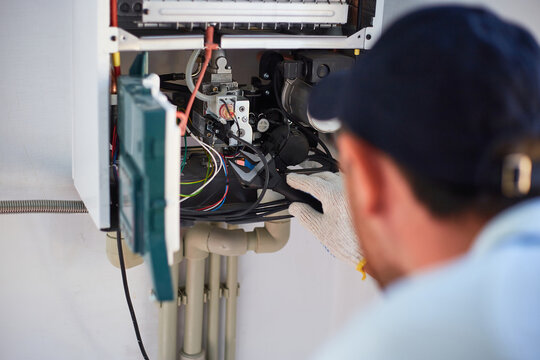
Upgrading equipment on a regular basis is essential for keeping a business competitive, efficient, and safe. However, the process can be costly and disruptive if not carefully planned out. This guide provides a complete breakdown of how to plan and budget for equipment upgrades in a way that makes sense for your business and minimizes risks.
Assess Your Current Equipment
Before deciding on upgrades, take a detailed inventory of your existing equipment. Include the following in your assessment:
Age and Condition: How old is the equipment, and is it nearing the end of its usable life? Is it still in good shape, or is it starting to wear out?
Performance: Does the equipment meet your current operational needs, or is it becoming a bottleneck?
Maintenance History: How often does it break down, and how much are you spending on repairs?
Compliance: Does it meet all current industry regulations and safety standards?
Write down these details for every major piece of equipment. This will help you prioritize which items need immediate attention and which can wait.
Define Your Business Needs
Determine why you are upgrading and how it aligns with your overall goals. Equipment upgrades should solve specific problems or create measurable improvements. Ask yourself questions like:
Expansion Plans: Do you need to strive to handle higher demand or enter new markets?
Efficiency Goals: How efficient is your current equipment? Could better equipment reduce operational costs or save time?
Safety Concerns: Are there hazards associated with outdated machinery that newer technology could eliminate?
Clearly defining your business needs in these specific areas will ensure that your investment directly impacts your bottom line.
Research Equipment Options
Once you know what you need, begin researching equipment options. Gather as much information as possible to make an informed decision, considering these aspects:
Features: Does the equipment offer the functionalities you need to address your business goals?
Reliability: Look for reviews or case studies to verify the equipment’s durability and performance.
Cost Breakdown: Consider not just the purchase price but also installation, training, maintenance, and eventual disposal costs.
New vs. Used: Consider the benefits of buying new equipment against the cost savings of purchasing used or refurbished items.
Keep a spreadsheet of your findings to easily compare the various options and choose what’s right for your business.
Build a Realistic Budget
A well-planned budget is the foundation of any successful equipment upgrade. Your budget should include:
Direct Costs: Include the purchase price, shipping, installation, and any upgrades to your facility to accommodate the equipment.
Ongoing Expenses: Be sure to factor in long-term expenses such as maintenance, energy consumption, spare/replacement parts, and training costs.
Financing Costs: Make note of any potential interest payments if you plan to take out a loan or lease the equipment.
Contingency Fund: Set aside 10–20% of the total cost for unexpected expenses such as delays, adjustments, repairs, or additional parts.
Breaking down your budget into these categories ensures that no hidden costs catch you off guard.
Explore Financing Options
Only some businesses have the cash flow to pay for expensive equipment outright. If that’s the case, explore financing options such as:
Leasing: Pay a monthly fee to use the equipment without owning it outright. Leasing often includes maintenance, which can save on operational costs.
Loans: Borrow money to purchase the equipment, then pay it off over time. This is ideal for equipment you’ll keep long-term.
Payment Plans: Some manufacturers and suppliers offer installment payment plans with little or no interest.
Each option has its advantages and drawbacks, so carefully calculate the long-term costs and decide what works best for your budget.
Plan Your Timeline
Timing your upgrades is just as important as budgeting for them. Upgrades should occur during periods of low activity to minimize disruptions to your business. Here’s how to plan your timeline effectively:
Evaluate Downtime: Choose a time when the equipment is least needed, such as off-season periods or slower months.
Implement in Phases: Upgrade one piece of equipment at a time to avoid overwhelming your operations.
Coordinate with Suppliers: Make sure that your supplier can meet your timeline and that there are no unexpected delays.
A clear schedule for incorporating your new equipment into your daily operations will do much to reduce downtime and ensure a smoother transition.
Train Your Team
Once the equipment arrives, don’t overlook the importance of training your team. Proper training can prevent accidents, reduce wear and tear, and ensure you get the most out of your investment. Include the following steps:
Schedule Training Sessions: Bring in experts or use supplier-provided resources to teach your team how to operate the new equipment.
Provide Manuals and Guides: Give employees access to detailed instructions that they can reference as needed.
Monitor Performance: Track how well your team adapts to the new equipment, and provide additional training if necessary.
Overlooking or skimping on training can lead to improper usage, accidents, or even damage to your new equipment.
Monitor and Evaluate Results
After the equipment is installed and in use, evaluate whether it’s delivering the benefits you expected. Consider the following:
Cost Savings: Are you spending less on maintenance and repairs compared to your old equipment?
Efficiency Gains: Are production times faster or workflows smoother?
Impact on Revenue: Have these upgrades contributed to better service and increased sales?
This step helps you understand the return on your investment and allows you to adjust your approach for future upgrades.
Business Benefits
For propane businesses, the benefits of planning and budgeting for equipment upgrades can be transformative. Upgraded delivery trucks, for example, can reduce fuel costs and ensure more timely deliveries. Modern storage tanks with advanced monitoring systems improve safety and allow you to manage inventory more efficiently. Streamlined scheduling software can enhance customer service and reduce unnecessary administrative burdens.
Properly planned upgrades not only improve daily operations but also strengthen your business’s reputation for reliability and professionalism. A propane business with well-maintained, modern equipment is better positioned to meet customer expectations, reduce costs, and stay competitive.