Propane Equipment Shortages: What You Need to Know
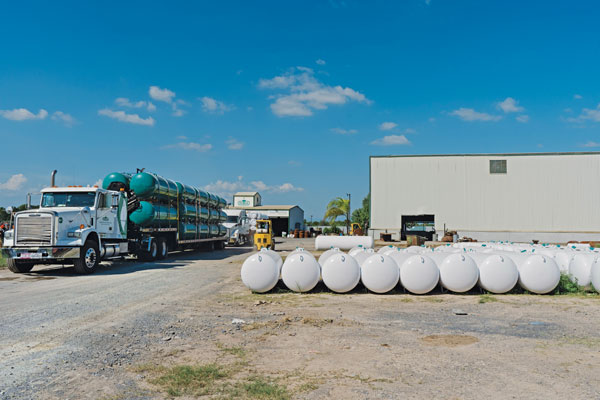
As a propane business owner, you may have noticed the growing challenge of getting the equipment you need on time. Propane equipment shortages and delays have become a serious issue, impacting businesses across the U.S. Here’s what’s behind these shortages and how you can manage the situation.
Understanding the Causes
The propane industry is not immune to global supply chain issues. Equipment manufacturers have faced delays due to disruptions in materials, transportation, and production processes. These issues have led to longer lead times and reduced availability of key equipment like tanks, regulators, hoses, and valves.
In addition, increased demand from other industries has put further pressure on the supply chain. With a high number of orders to fulfill and limited resources, suppliers need help to meet the needs of propane businesses in a timely manner.
How Delays Affect Your Business
When you can’t get the equipment you need, it can slow down your operations. Whether it’s installing new tanks for customers or maintaining your existing equipment, delays can affect your ability to provide reliable service. This, in turn, can lead to unhappy customers and missed opportunities for growth.
In some cases, businesses have to turn to less familiar or more expensive suppliers, which can increase costs and create new logistical challenges. The longer you wait for key pieces of equipment, the harder it becomes to maintain your competitive edge in the market.
Staying Ahead of the Problem
While the situation may seem out of your control, you can take steps to manage these shortages. First, it’s important to communicate with your suppliers regularly. By staying informed about potential delays, you can adjust your plans and set realistic expectations for your customers.
Another option is to diversify your suppliers. Instead of relying on a single source, work with multiple vendors to improve your chances of finding available equipment. This strategy can help you avoid being stuck when one supplier experiences issues.
Planning for the Future
Looking ahead, it’s a good idea to plan further in advance than you might have in the past. Ordering equipment earlier than usual can help you avoid major disruptions to your operations. Keep an eye on your inventory levels and make sure you have enough spare parts and equipment to last through any unexpected delays.
Additionally, consider adjusting your business model to accommodate these changes. Offering rental equipment or maintenance services, for example, can provide alternative revenue streams while you wait for new equipment to arrive.
Key Takeaways
Equipment shortages and delays are a real challenge, but with the right approach, you can continue to meet your customers’ needs. Stay flexible, keep communication open with your suppliers, and plan ahead in order to minimize the impact on your business. By preparing now, you’ll be better able to handle future disruptions and continue providing excellent service to your customers.